製図から、切断、穴あけ、曲げ、組立、溶接、塗装仕上げまで
一貫した加工ラインを持ち、ワンストップサービスが可能です
板金加工の流れ
Order Flow
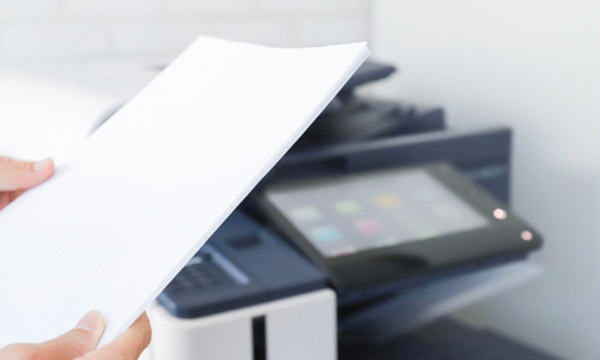
received order受注
メール、FAXにてご注文書を受理後、生産管理システムに入力し作業指示書を作成します。 製作図面と作業指示書(バーコード付き)を現場に出図して、各工程での作業をPCやiPodで進捗を取ることにより、事務所にいながらリアルタイムに進捗状況を把握できます。 実績の集計・活用もでき、現場の“見える化”を飛躍的に高めています。
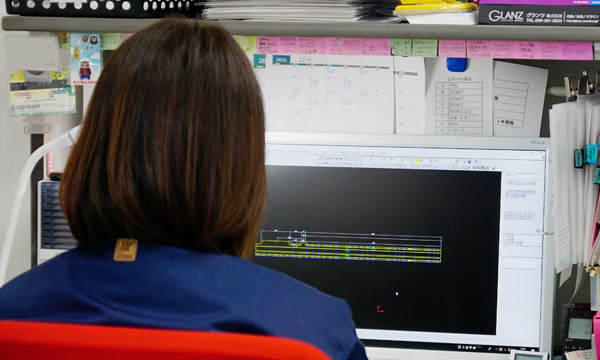
programmingプログラミング
紙図面、PDF図面を元にAP100・2D-CAD(図面展開)、CAM(金型割り付け)を行い、加工データを作成します。 ブランク、ベンダー、タップ等の工程で各機械に加工データを読み込みことですぐに加工を始めることが出来ます。 CAD、PCLデータを頂ければデータ作成もスピーディーに。
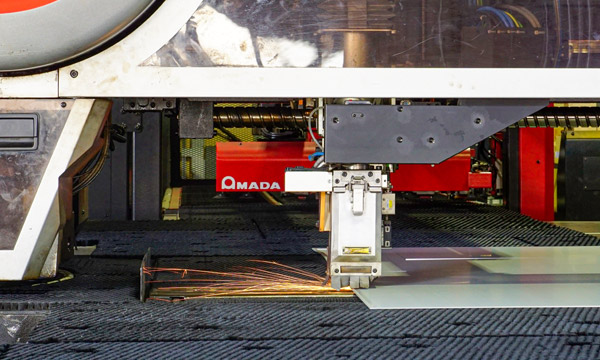
blankブランク
ブランクとは、精密板金加工で最初に行われる加工工程のことで、 抜き加工とも呼ばれます。 ブランク加工には、ターレットパンチプレス加工とレーザー加工の2種類がありますが、加工工数がかからない為ターレットパンチプレス加工が一般的です。 製品の形状・特性に適した加工機で素材の切断や穴あけなどの加工を行います。
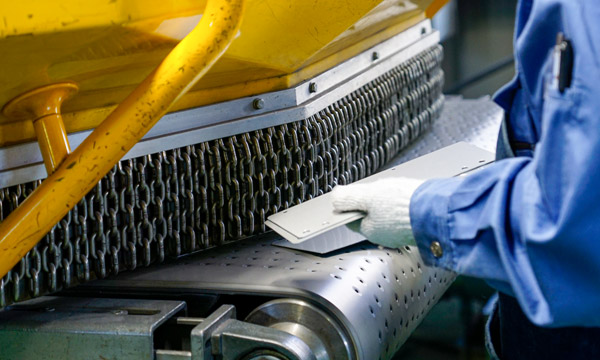
deburringデバリング
デバリンクはブランク加工時に発生する出っ張りやギザギザ、日本語では「かえり」ともいいますがそれらを除去する工程になります。 通常、グラインダーを使い手作業で除去していきますが、弊社では自動バリ取り機を使用して作業時間を短縮出来、エッジ部は非常に均一なR面取り加工が可能で2次バリも発生しません。
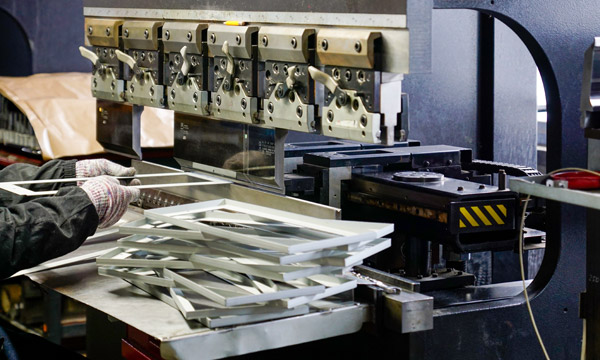
benderベンダー
ブランク加工で展開形状の製品外形及び穴加工等を行った物をパンチ(上金型)とダイ(下金型)を用い所定の角度に曲げ立体的に仕上げる加工です。 弊社ではより多彩な曲げ加工を行う為標準型はもちろん、特殊金型を保有しております。曲げ加工の段取りレス・長時間運転を実現する高精度ベンディングロボットシステムを併用することで変種変量にも対応可能です。
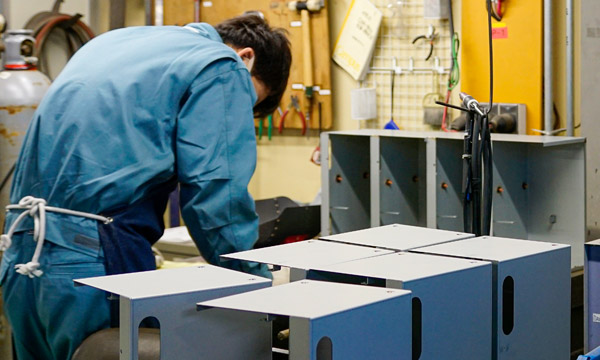
assemblyアッセンブリ
MIG・TIG・YAG溶接機を使用することで鉄・ステンレス・アルミなど様々な材質の溶接が可能です。 短時間で接合可能なスポット溶接機、ロボットでの溶接などを併用することで、お客様の要望される形状の組立てを実現させています。
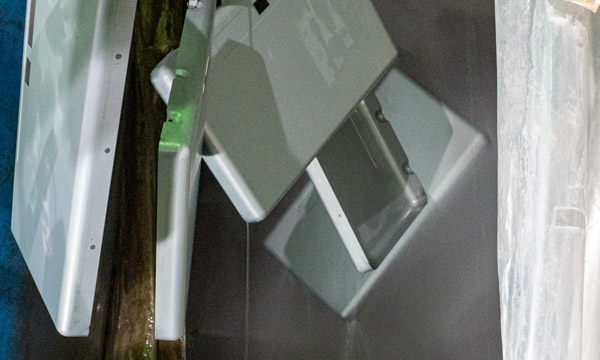
cleaning洗浄
弊社では塗装前の下地処理を自動洗浄ラインで行っております。短時間で満遍なく脱脂からりん酸鉄化成処理を行うことで、被塗物に優れた耐食性・密着性を与え、塗装工程の安定した仕上がりを支えています。
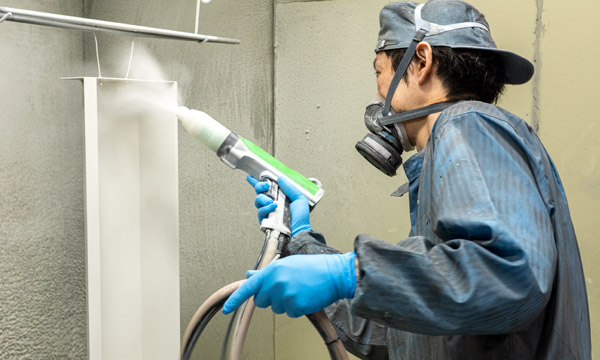
painting塗装
スプレーガンでの吹付塗装や粉体塗装を行った後に乾燥炉で100~200℃の範囲で硬化させます。最新式の塗装ブース内で塗装することで、吹付時に発生する塗料の有機溶剤を適切に屋外へ排出させ、被塗物への粉塵などの付着を防止し、人体への衛生環境を守っています。 鉄・ステンレス・アルミにも塗装可能で、大量の物件も塗装ロボットで対応出来ます。
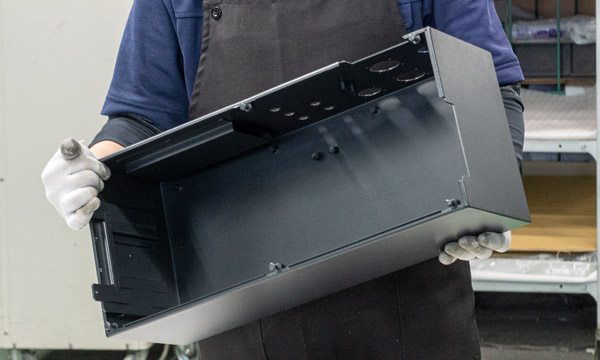
inspection検査
弊社では板金加工が終わった時点で行う中間検査と、塗装の仕上がり確認する外観検査の二ヵ所で検査を行っています。 中間検査ではノギスやマイクロゲージ、3D検査装置を用いて図面通りに仕上がっているかを確認します。外観検査ではお客様の要求通りに塗装が仕上がっているかを一つ一つ目視で確認します。 もし不具合が見つかった場合は、製品の不良発生に関する分析、工程の見直しなどを行い、製造プロセスの管理や改善を図ります。